Steel cut to length line processing is an advanced mechanical technology for metal sheet processing. It uses a series of precision equipment to unwind, flatten and shear metal coils to meet the production needs of different industrial fields.
With the continuous advancement of global industrialization, the application field of steel ctl lines has gradually expanded, and the demand and application direction of steel ctl lines in different countries are also different. This article will discuss in detail the application fields, main components, workflows and characteristics of customized steel cut to length machines.
Application fields of steel ctl lines
Global demand status
There is a huge demand for steel cut to length machines in the world, especially in the manufacturing, construction, automotive and electronics industries. With the continuous advancement of technology and the improvement of production efficiency, more and more companies choose to use steel ctl lines to improve production efficiency and product quality.
Application focus in different countries
Although the basic functions of steel cut to length machines are similar, the application fields of different countries are also different due to differences in industrial structure, market demand and technical level.
1. United States: The manufacturing industry in the United States is mainly high-tech and high-value-added products. Therefore, steel ctl lines are widely used in high-precision metal processing in the automotive, aerospace and electronics industries. The US market has high requirements for the automation and intelligence of steel cut to length machines.
2. Germany: Germany is famous for its precision manufacturing, and steel ctl lines play an important role in machinery manufacturing, mold manufacturing and the automotive industry. German companies tend to use high-efficiency and high-precision steel ctl lines to meet strict quality standards.
3. India: With the rapid development of the economy, India's manufacturing industry has gradually risen, and the application of steel ctl lines in the construction, automobile and home appliance industries has gradually increased. Due to the diversification of market demand, customized steel ctl lines are popular in the Indian market.
4. Southeast Asia: The manufacturing industry in Southeast Asian countries is developing rapidly, and steel ctl lines are gradually becoming popular in the metal processing and construction industries. Companies in these countries usually seek cost-effective steel ctl lines to meet the growing market demand.
Main components of steel ctl lines
The performance and efficiency of steel cut to length lines mainly depend on their various components. Generally speaking, steel ctl lines are mainly composed of the following precision components:
1. Decoiler: used to unfold metal coils to ensure smooth transmission and processing of coils.
2. Leveler: Through mechanical leveling, the waves and bends of the coil are eliminated to ensure the accuracy of the shearing process.
3. Cut to length machine: It is the core part of the shearing line and is responsible for shearing the flattened metal sheets. The accuracy and speed of the cut to length machine directly affect the quality of the product.
4. Waste collection device: It is used to collect the scraps generated during the shearing process to keep the working environment clean.
5. Conveyor belt: It is used to transport the processed metal sheets to the subsequent process or finished product stacking area.
6. Stacker: It is used to neatly stack the sheared metal sheets for subsequent handling and storage.
Workflow of steel cut to length machine
1. Uncoiling: Place the metal coil on the decoiler and unfold it automatically.
2. Leveling: After the leveling machine, the surface flatness of the metal coil is improved, ready for shearing.
3. Shearing: The flattened metal sheet enters the shearing station for precise shearing to form the required size and shape.
4. Waste treatment: The waste generated during the shearing process is collected and treated by the waste collection device.
5. Conveying and stacking: The sheared metal sheets are transported to the stacking table through the conveyor belt and neatly stacked for subsequent processing.
6. Quality inspection: In some cases, the shearing line will also be equipped with a quality inspection system to check the size and quality of the sheared metal sheets.
Customized steel ctl line
In the market, customized steel cut to length machines are increasingly favored by customers, especially KINGREAL SLITTING's steel cut to length machines, which have won wide acclaim for their flexible customization capabilities. Each steel ctl line is designed according to the specific needs of the customer, and this personalized service provides customers with higher value.
Heavy gauge cut to length line
Customer background: A large heavy industrial enterprise, mainly engaged in steel processing, produces metal raw materials with thickness exceeding that of most steel cut to length machines on the market.
Customized solution: KINGREAL SLITTING designed a heavy duty cut to length line capable of processing 6-20mm thick metal sheets according to customer needs. The equipment is equipped with high-strength shearing tools and an optimized shearing system to ensure efficient and stable shearing effects under high loads.
Effect: The customized steel cut to length machine not only improves production efficiency, but also reduces equipment failure rate. Customers said that production capacity has increased by 30% after use.
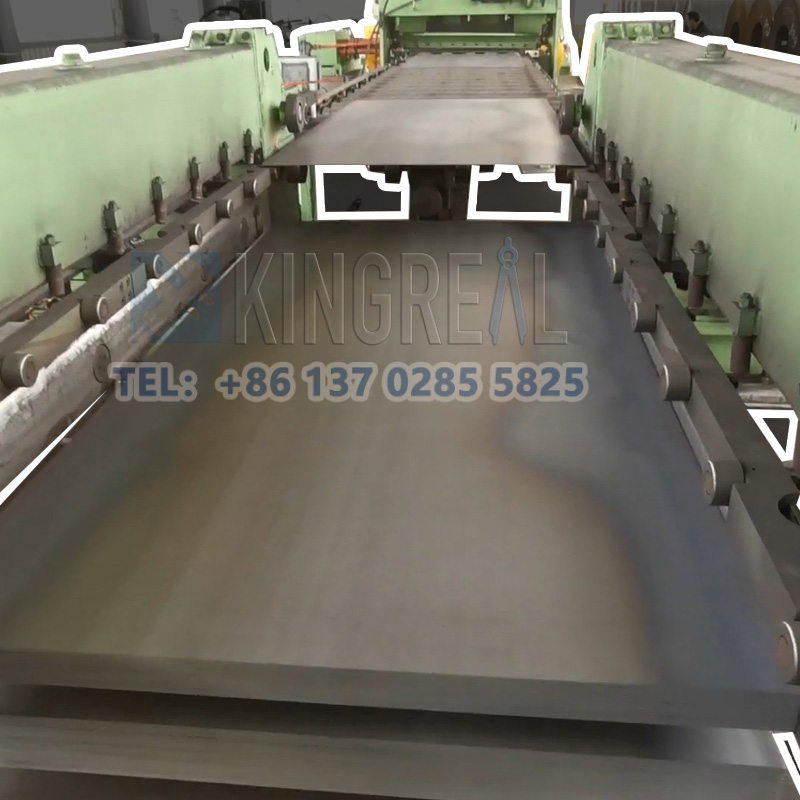
Light gauge cut to length line
Customer background: A certain electronic component manufacturer needs to process thin metal coils with high precision.
Customized solution: Engineers designed a light gauge cut to length line that can handle a minimum of 0.3mm thick metal, using high-precision shearing technology to ensure smooth shearing edges without burrs.
Effect: This customized steel ctl line greatly improves production flexibility and meets customers' diverse product needs. Customers said that the product qualification rate has reached more than 98%.
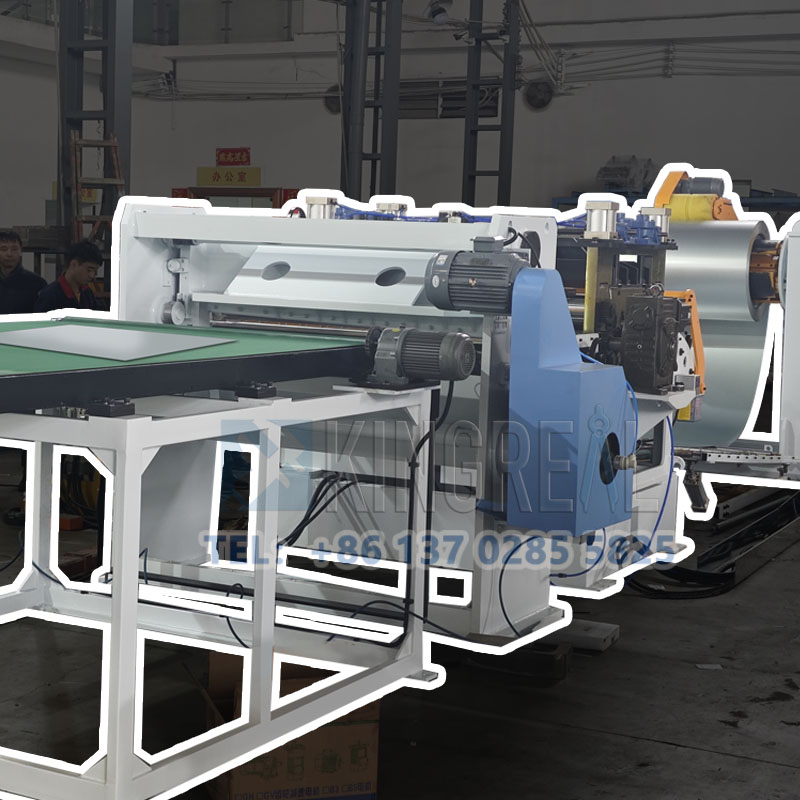
Fly shearing cut to length machine
Customer background: A certain automotive parts manufacturer has extremely high requirements for production efficiency.
Customized solution: KINGREAL SLITTING designed a fly shearing cut to length line for the customer, which can be sheared without stopping, and the maximum shearing speed can reach 80m/min. The equipment integrates an advanced automatic control system to achieve unattended operation.
Effect: Through the use of the flying shearing cut to length line, the customer's production efficiency has increased by 50%, and the labor cost has been greatly reduced.
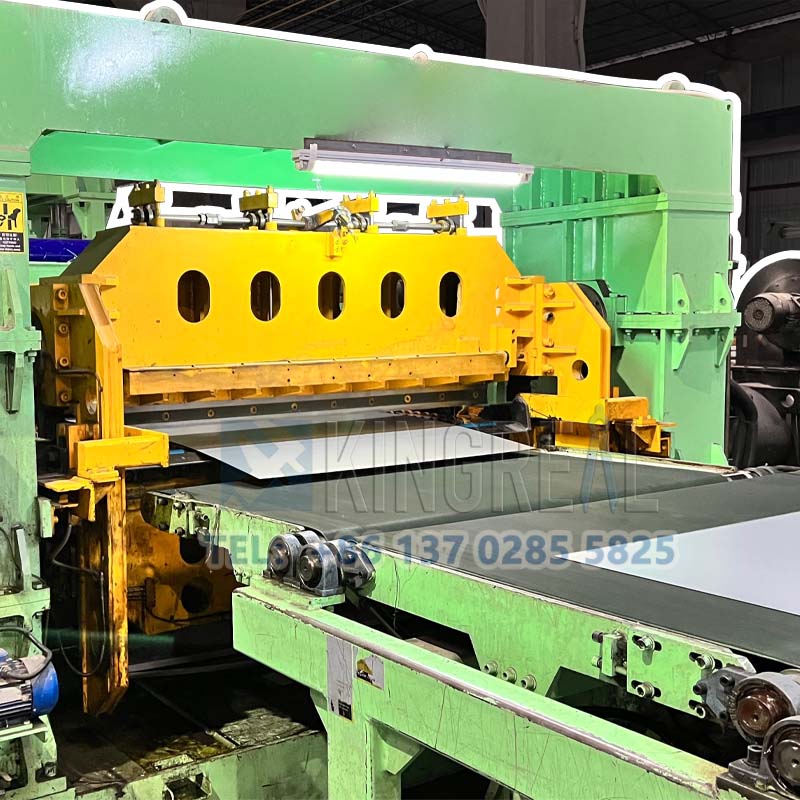
Customer background: A small factory needs a steel ctl line with a small footprint due to space constraints.
Customized solution: KINGREAL SLITTING designed a compact ctl line for it. Although it is fully functional, it occupies a small area and is suitable for use in limited spaces.
Effect: The customer has achieved efficient metal sheet shearing in a smaller factory space, greatly improving production flexibility, and the customer is very satisfied with it.
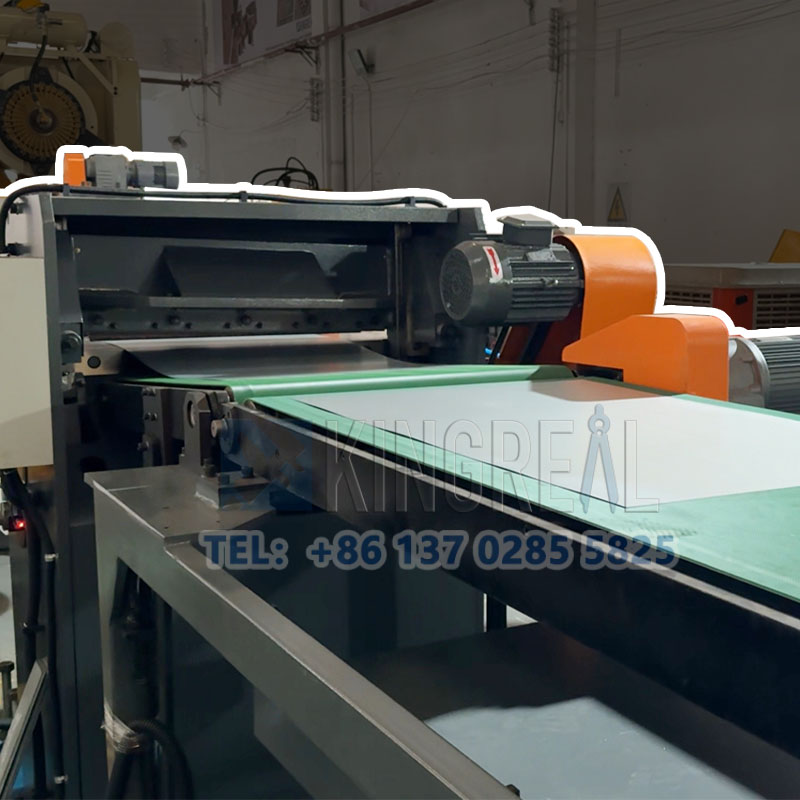