In modern manufacturing, the dual slitter head slitting line is a widely used equipment, especially in the field of metal processing. It can slit large rolls of metal coils into strips to meet the needs of different products. However, to ensure the efficient operation of the dual slitter head slitting machine, the installation and adjustment of the knife is crucial.
In this article, KINGREAL SLITTING will discuss with you the relevant knowledge of the knife seat of the dual slitter head slitting equipment to help users better use the dual slitter head slitting machine.
Knife seat coordination of the dual slitter head slitting equipment
In the dual slitter head slitting machine, the upper and lower knife seats are key components for supporting and fixing the knives. Their coordination directly affects the stability and cutting effect of the knife. The following are the adjustment steps of the upper and lower knife seats:
1. Lower knife seat adjustment
- Height adjustment: First, by adjusting the height of the lower knife seat, ensure that the knife is parallel to the work surface or at an angle set as needed. Be sure to ensure that the lower knife seat is firmly fixed to the base of the dual slitter head slitting equipment and follow the instructions in the operating manual for adjustment.
2. Upper knife seat adjustment
- Position adjustment: Next, adjust the position of the upper knife seat so that the knife corresponds to the lower knife seat. The upper knife seat is usually movable on the dual slitter head slitting machine so that the position of the knife can be adjusted as needed. Keep the upper knife seat stable and tightly fix the knife.
3. Knife installation
- Knife fixation: Insert the knife into the upper and lower knife seats, and make sure that the knife is firmly fixed on both knife seats. According to the cutting requirements, select the appropriate knife and install it correctly to ensure the accuracy and stability of the cutting.
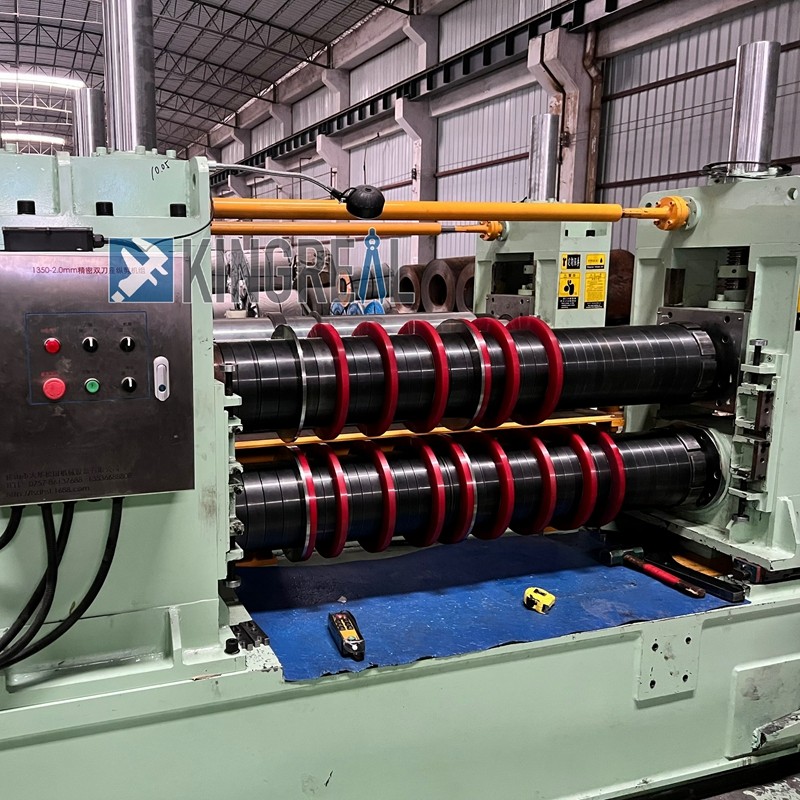
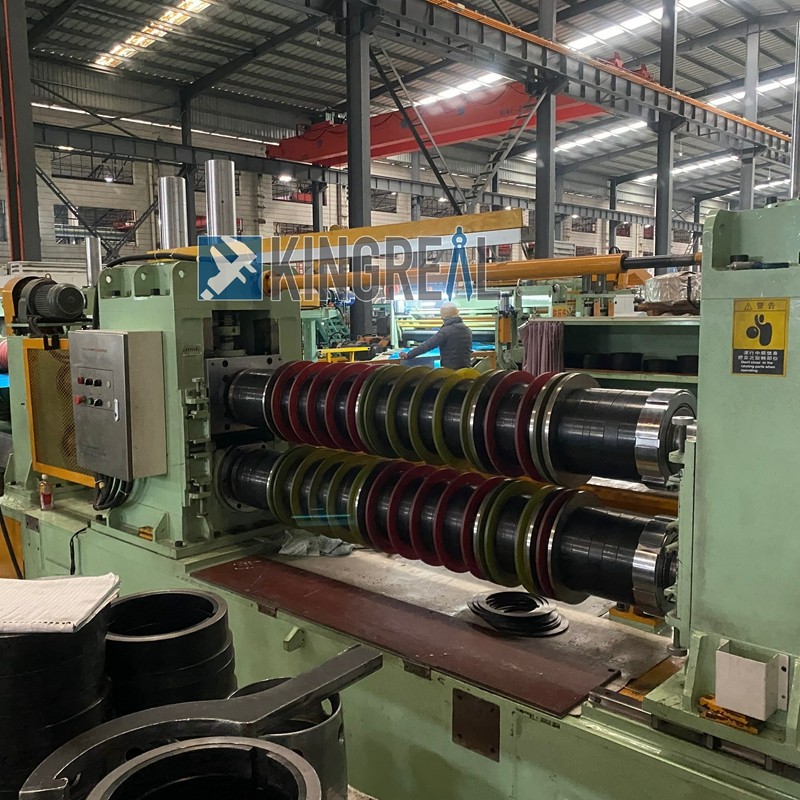
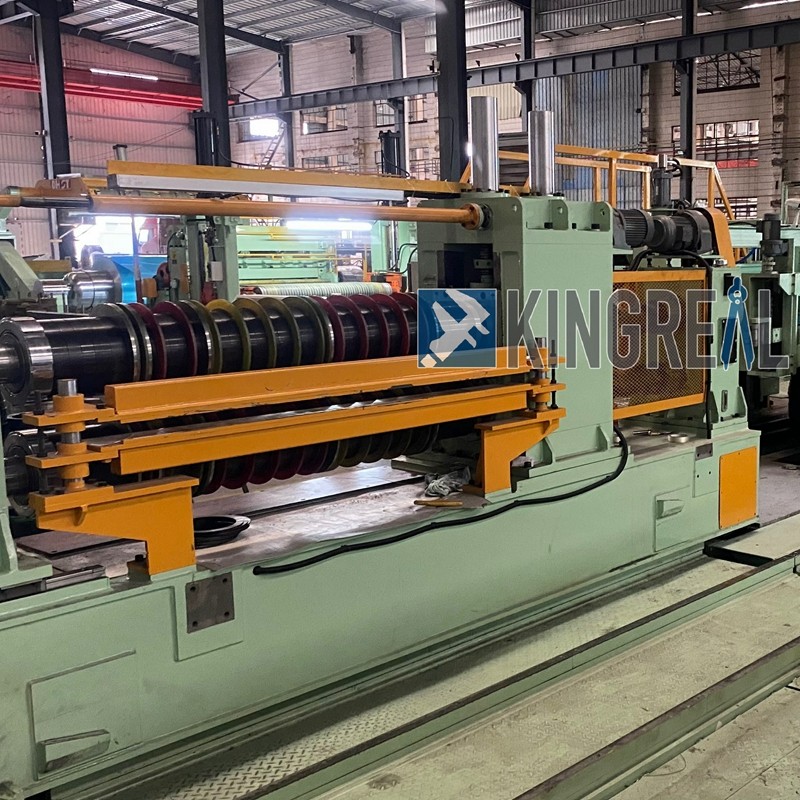
It is important that the matching adjustment of the upper and lower knife seats should be carried out according to the specific dual slitter head slitting line model and the manufacturer's guidance. Follow the instructions in the operating manual to ensure the safety and effectiveness of the cutting process.
Blade material of dual slitter head slitting equipment
The material selection of dual slitter head slitting machine blades has a significant impact on the cutting effect. Common blade materials include:
- High-speed steel: such as W18Cr4V, SKH, SKD-11, etc., have good wear resistance and cutting performance, and are suitable for high-speed cutting operations.
- Die steel: such as Cr12MoV, LD, H13, etc., with excellent wear resistance and hardness, suitable for heavy-load slitting processing.
- Carbide: such as YG (tungsten-cobalt alloy) and YW (tungsten-titanium alloy), with extremely high hardness and wear resistance, suitable for processing high-hardness materials.
- Ceramic materials: such as Al2O3-based ceramics and Si3N4-based ceramics, have good wear resistance and high temperature resistance, but are relatively fragile.
- Diamond materials: including natural diamonds and artificial polycrystalline diamonds (PCD), suitable for cutting extremely high-hardness materials, with strong wear resistance.
These materials undergo a heat treatment process to improve the hardness and wear resistance of the blades, ensuring that the blades maintain good cutting performance during the slitting process.
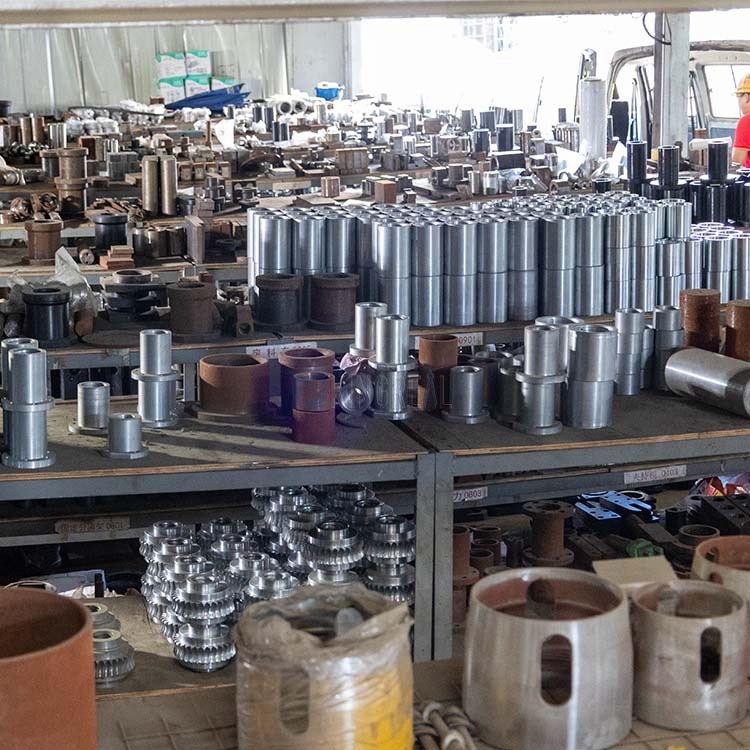
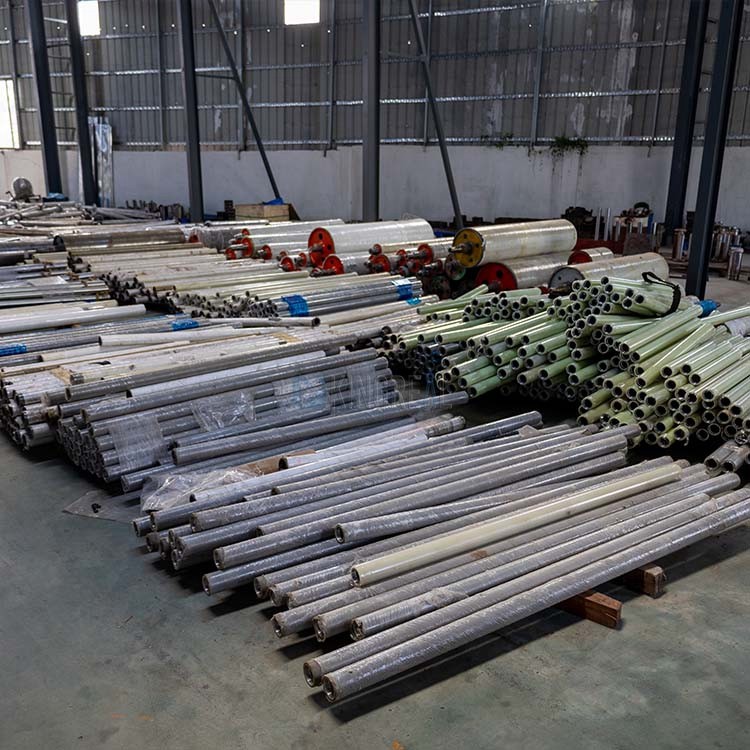
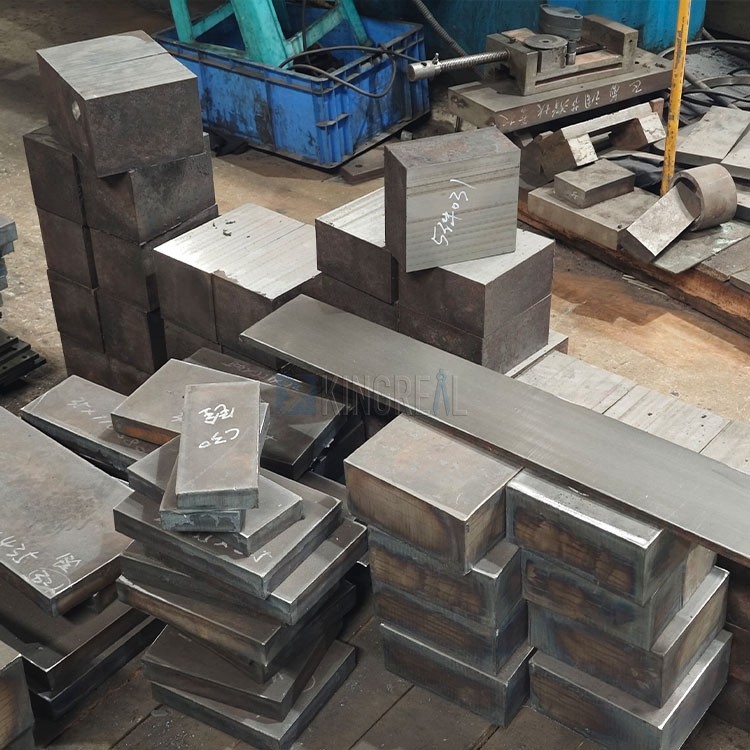
Dual slitter head slitting equipment tool installation tutorial
Installing the tool is an important step in using the dual slitter head slitting machine. The following is the specific installation process:
1. Prepare tools: prepare wrenches, screwdrivers and other tools.
2. Find the tool slot: Find the tool slot or fixture on the dual slitter head slitting line.
3. Remove the old tool: If you already have an old tool, use a wrench or screwdriver to loosen the tool nut or fixing screw. If it is a brand new tool, skip this step.
4. Remove the old tool: Remove the old tool from the slot or device.
5. Install the new tool: According to the tool design, put the new tool into the slot to ensure that it is correctly positioned and stable, and the sharp edge of the tool should face the material to be processed.
6. Fix the tool: Use a wrench or screwdriver to tighten the tool nut or fixing screw to ensure that the tool is firm, but not too tight.
7. Check the installation: Check the installation of the tool to ensure that the tool is firmly fixed and not loose.
8. Make adjustments and calibrations: After completing the tool installation, make necessary adjustments and calibrations to ensure that the position and angle of the tool meet the requirements.
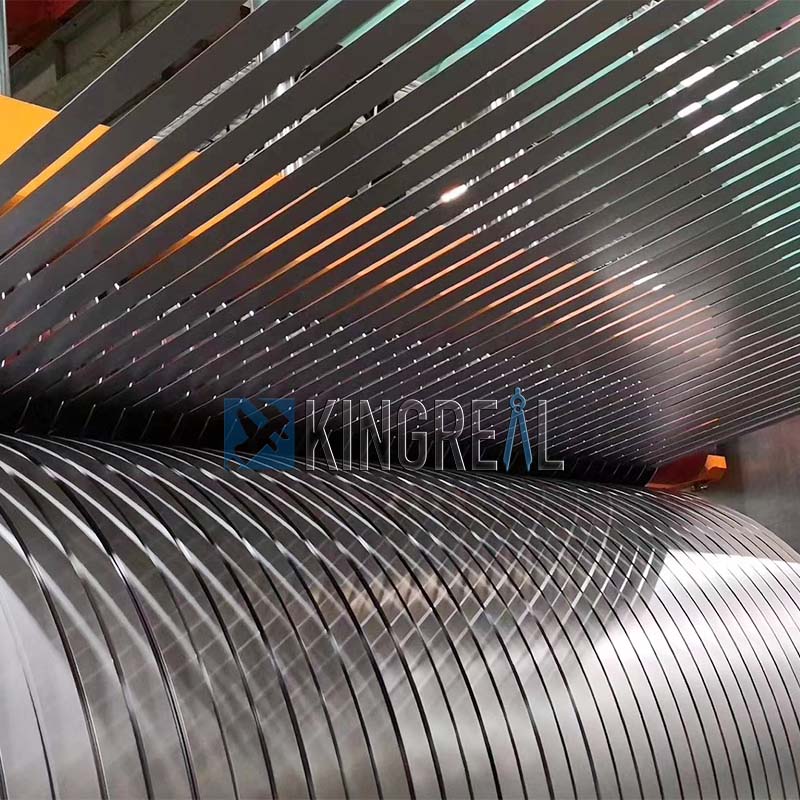
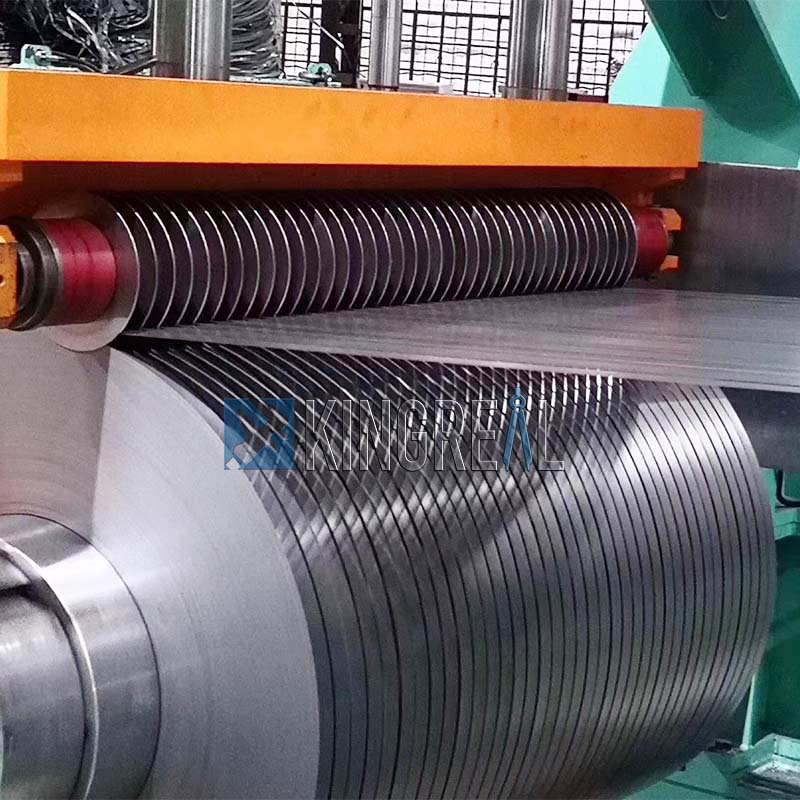
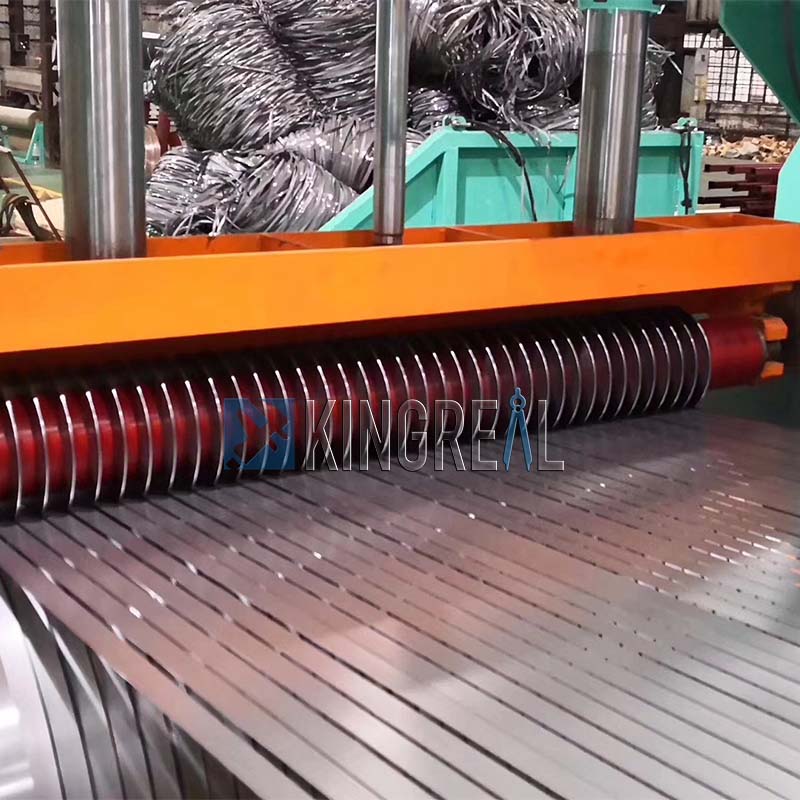
Tips for fast and accurate adjustment of dual slitter head slitting line tools
Correctly adjusting the dual slitter head slitting equipment tool is the key to ensuring cutting accuracy. Here are some adjustment tips to help you quickly and effectively complete the tool adjustment:
1. Determine the cutting size
Before adjusting the tool, you should first determine the required cutting size, including length and width. The cutting requirements of each material are different, so the tool must be adjusted according to actual needs.
2. Adjust the side knife
The side knife is the main cutting component when the dual slitter head slitting machine cuts materials. It is necessary to determine the inclination angle of the side knife and then adjust the position to maintain the correct blade spacing and cutting accuracy.
3. Adjust the main knife
The cutting depth of the main knife affects the size after cutting, so it must be adjusted to the correct position to ensure cutting accuracy. Adjust the cutting depth by lifting the knife seat to ensure that the knife teeth are in good condition.
4. Adjust the back knife
The back knife is used to support the material for cutting. When adjusting, the blade and the side knife should be on the same plane to ensure neat and smooth cutting.
5. Lubrication and refueling
When adjusting the tool, all moving parts should be lubricated in time to reduce wear and increase the service life of the dual slitter head slitting equipment. Pay attention to the control of oil volume to ensure that lubrication is in place.
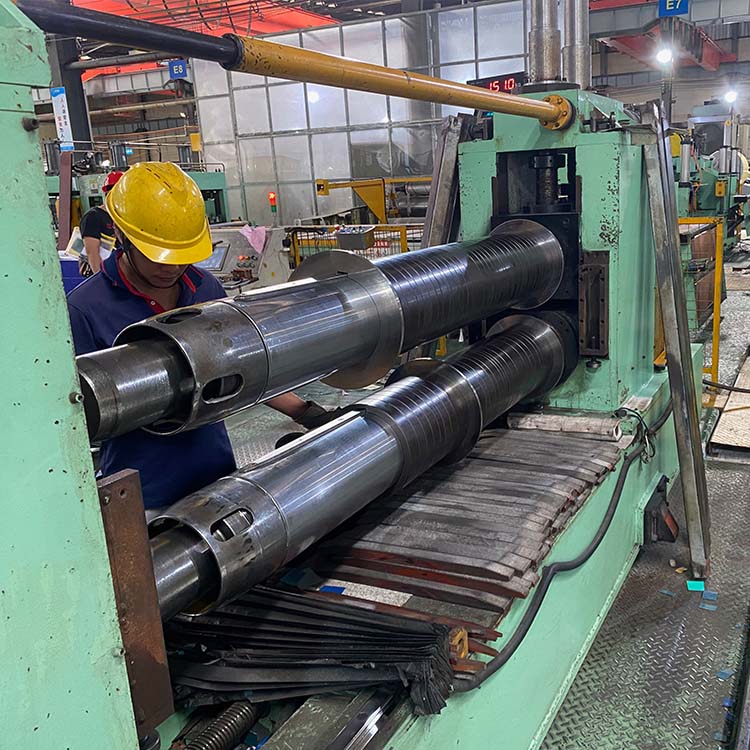
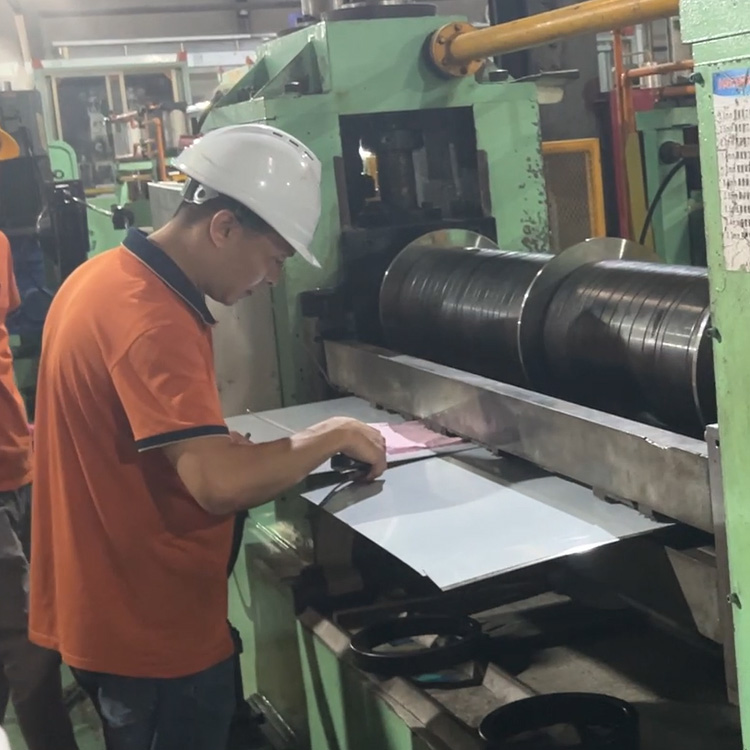
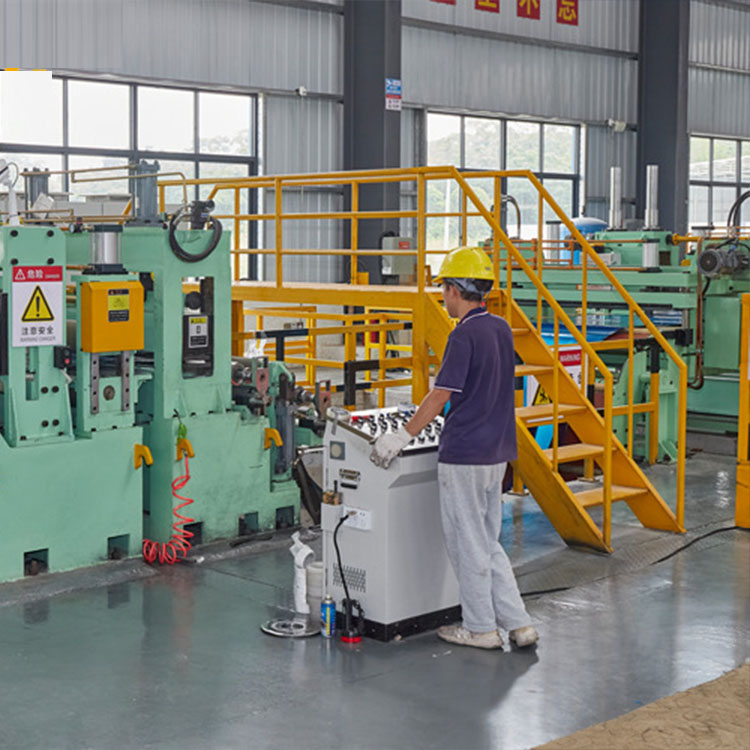
Knife arrangement method of dual slitter head slitting line
The knife arrangement method ofdual slitter head slitting machine directly affects the cutting effect. The following are several common knife arrangement methods:
- Regular knife arrangement: Arrange the blades at equal distances according to a certain spacing, which is suitable for situations where equal-width strip products are required.
- Staggered knife arrangement: Adjacent blades are staggered to effectively reduce vibration and impact during cutting and improve stability.
- Gradient knife arrangement: The spacing and size of the blades have a gradual change, which is suitable for obtaining strip products of different widths.
- Short-long-short knife arrangement: The blades are arranged in the order of short-long-short to reduce vibration during cutting.
- Special shape knife arrangement: According to processing requirements, the blades can be installed in special shapes such as wavy and serrated to meet specific processing requirements.
The selection and adjustment of these knife arrangement methods should be carried out according to the processing materials and product requirements. In actual operation, it is recommended to select the appropriate knife arrangement method according to the specific situation and adjust it according to the actual effect.