1. Definition of cut to length line
Metal cut to length machine is the most widely used metal plate shearing equipment in various industrial sectors. It is mainly used to cut the straight edges of metal plates of various sizes. The main function of the cut to length line is the metal processing industry. The products after shearing are widely used in aviation, light industry, metallurgy, chemical industry, construction, shipbuilding, automobile, electricity, electrical appliances, decoration and other industries.
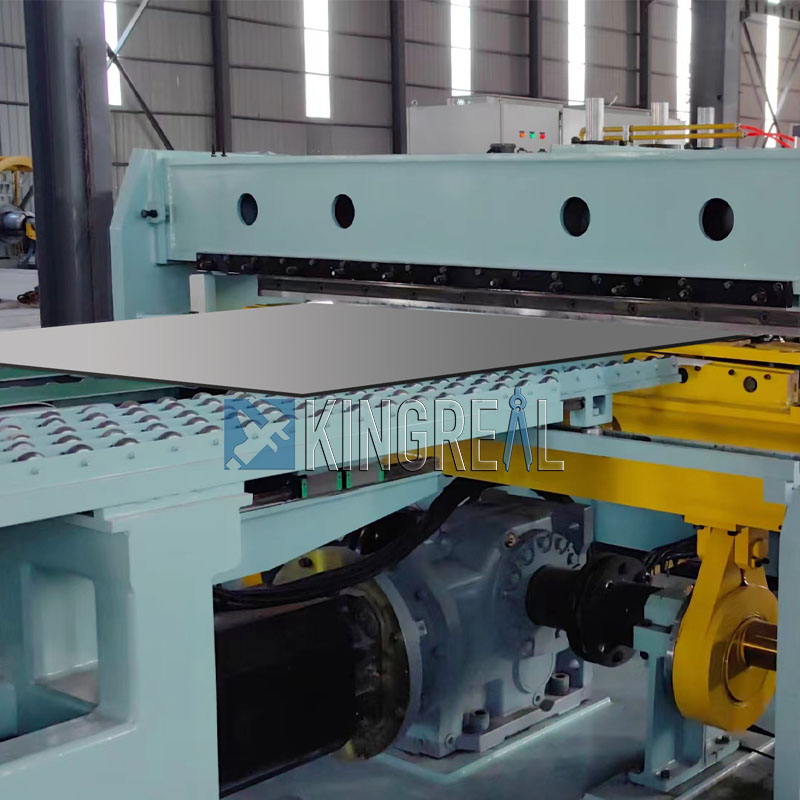
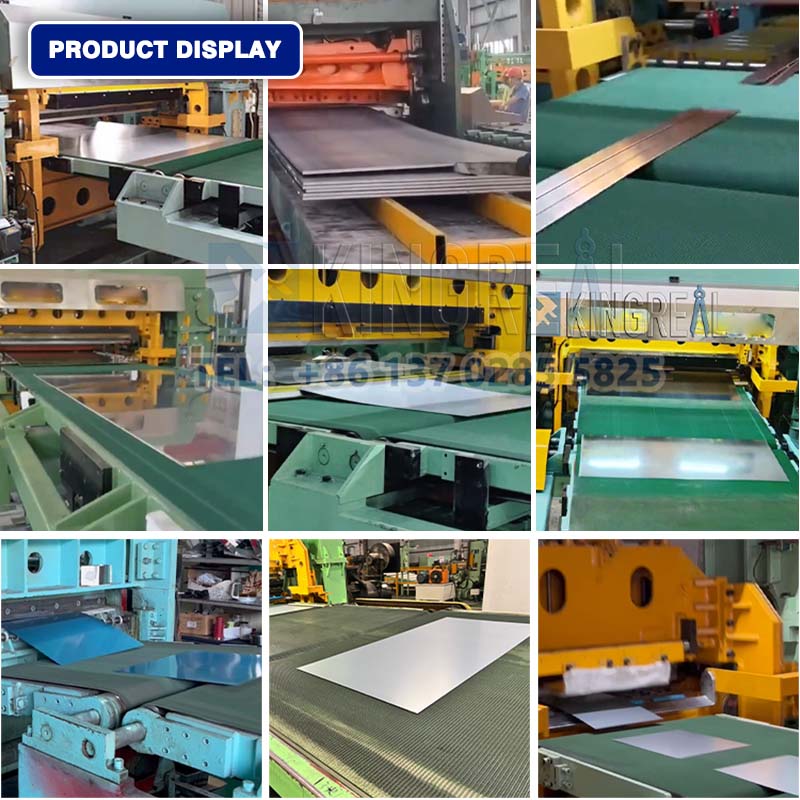

2. Different shearing methods of cut to length line
In the production process of metal cut to length machine, shearing is one of the key links, which directly affects the dimensional accuracy, edge quality and production efficiency of the finished product. According to different production requirements and process characteristics, cut to length lines usually use four shearing methods: fixed shearing, flying shearing, rotary shearing and swing shearing. The following is a detailed analysis of the main meanings of these shearing methods and their differences:
2.1 Fixed Shearing
Definition
Fixed shearing is the most traditional shearing method, which means that during the production process, the shearing equipment is in a fixed position and the shearing action is performed when the material stops moving. That is, when the metal sheet is transmitted to the preset length, the production line will pause, and the sheet will continue to be transmitted after the shearing machine completes the shearing action.
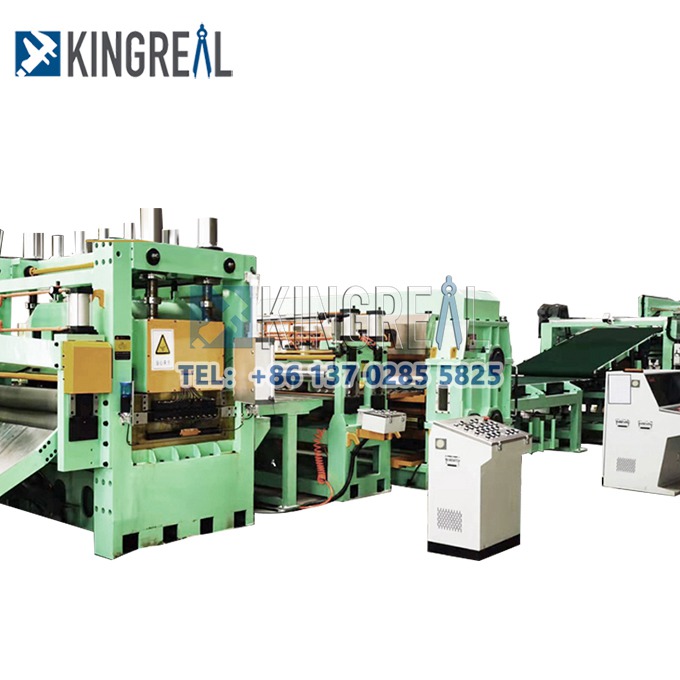
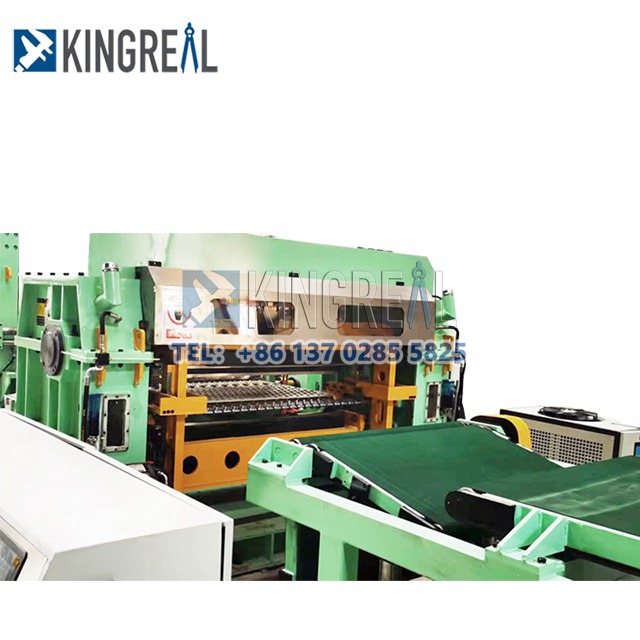
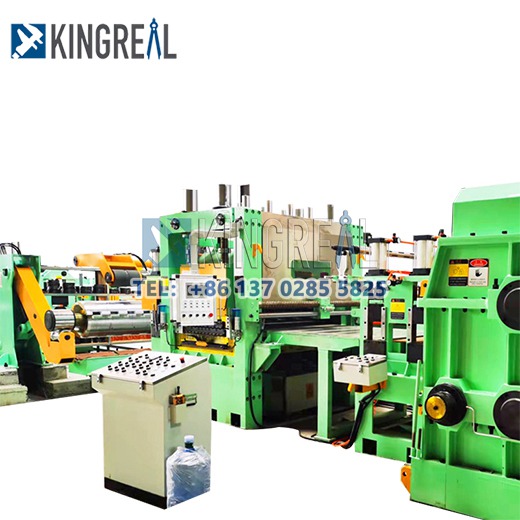
Features
- High precision: Since the plate is in a stationary state during shearing, the shearing precision is high and the error is small.
- Suitable for low-speed production: The shearing efficiency of the fixed shear is limited by the start-stop speed of the production line, and is usually used in medium and low-speed production scenarios.
- Simple equipment structure: The fixed shearing cut to length line has a relatively simple structure, low cost and easy maintenance.
Application scenarios
Suitable for scenarios with high requirements for shearing precision but low production speed, such as medium and thick plate shearing or small batch production lines.
2.2 Flying Shearing
Definition
Flying shearing is a dynamic shearing method, in which the shearing equipment can complete the shearing action while the plate moves. The shearing knife moves synchronously with the plate, and returns to the initial position after shearing is completed, ready for the next shearing.
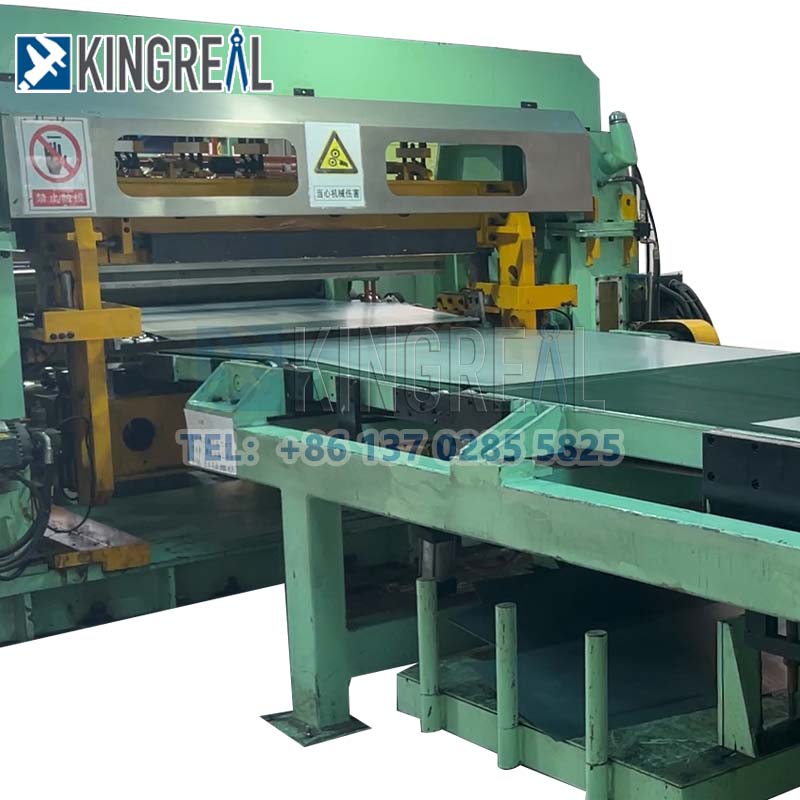
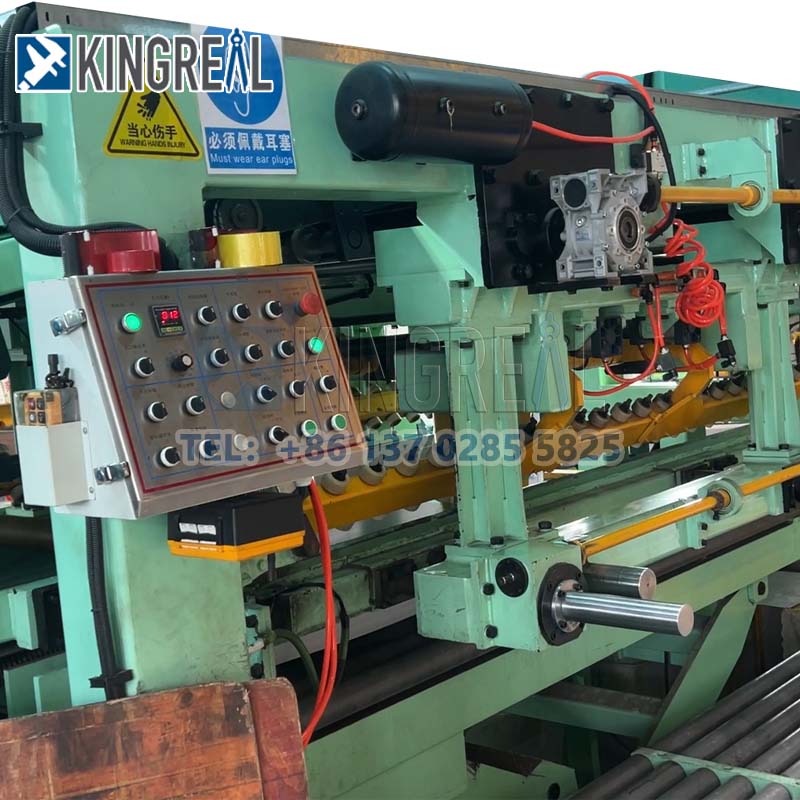
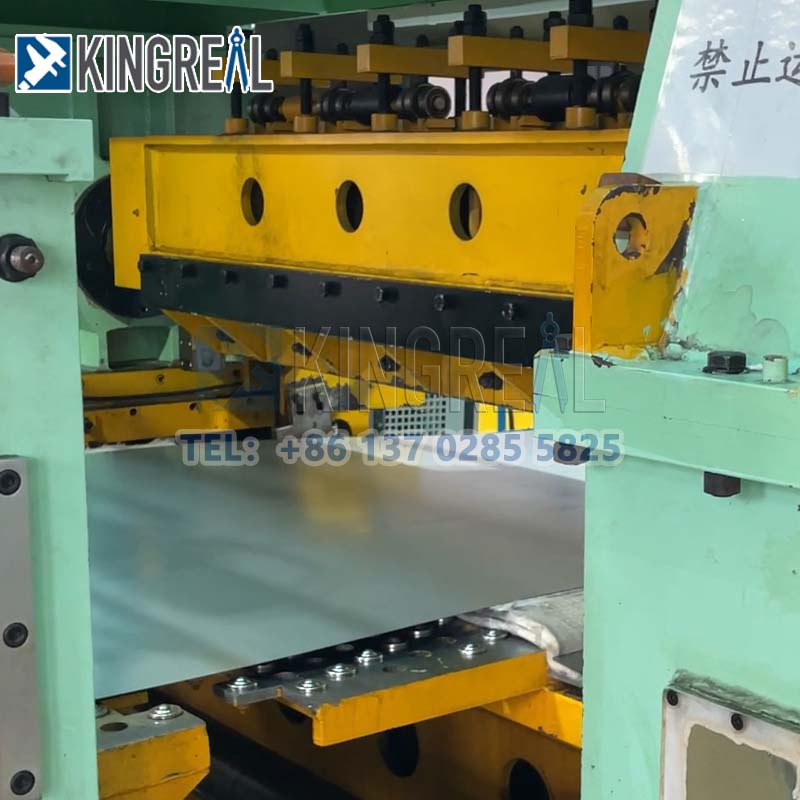
Features
- Suitable for high-speed production: The flying shear can complete shearing without stopping the line, which greatly improves production efficiency.
- High requirements for synchronous control: The movement speed of the shearing knife and the plate conveying speed must be highly consistent, and the control system of the equipment is required to be high.
- Strong adaptability: It can be used to shear plates of different lengths to meet diversified production needs.
Application scenarios
Commonly used in high-speed production lines, such as continuous shearing of thin plates or coil processing cut to length lines.
2.3 Rotary Shearing
Definition
Rotary shearing is a method of shearing by rotating a tool. The shearing tool moves in a circular or arc-shaped trajectory, completing the shearing action while the metal plate moves continuously.
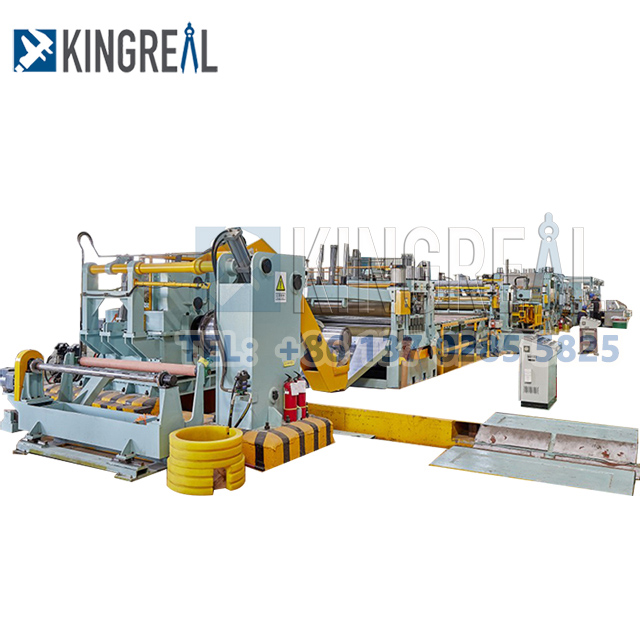
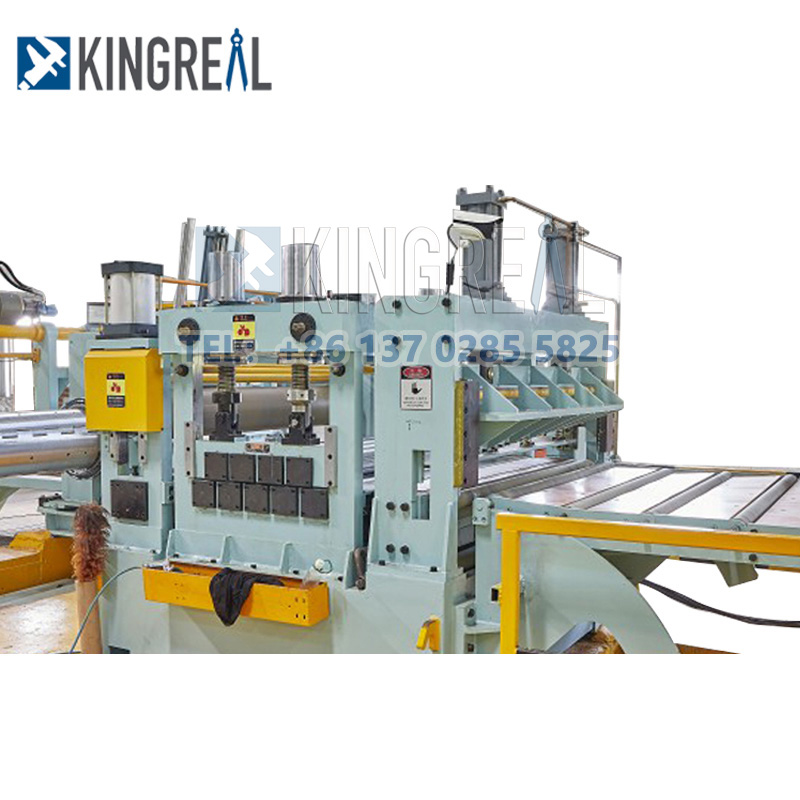
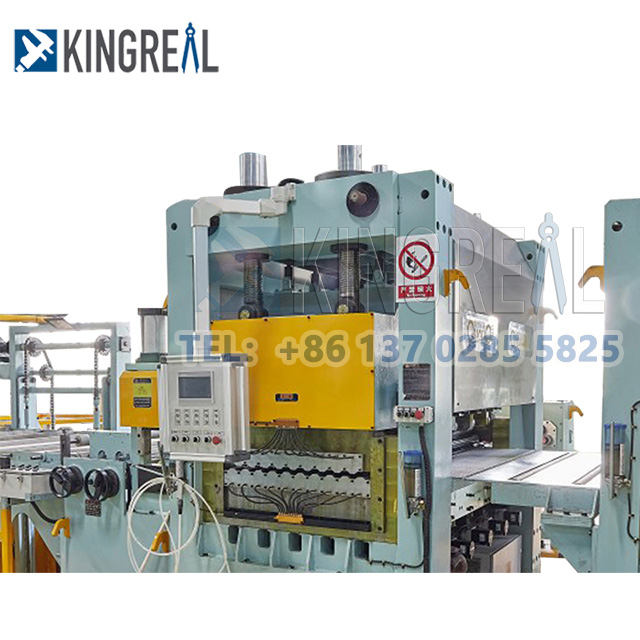
Features
- High speed and high efficiency: Rotary shears can complete shearing actions at extremely high speeds, suitable for large-scale production.
- Suitable for continuous production: Rotary shears do not need to interrupt the movement of the plate to maintain the continuity of the metal cut to length machine.
- High shearing quality: The design of the rotary tool makes the shearing edge smoother and reduces burrs.
Application scenarios
Suitable for ultra-high-speed thin plate shearing or scenes with high shearing quality requirements, such as metal sheet processing in the automotive industry.
2.4 Swing Shearing
Definition
Swing shearing is a method of shearing by swinging a tool. The shearing tool swings around a fixed point to shear the plate.
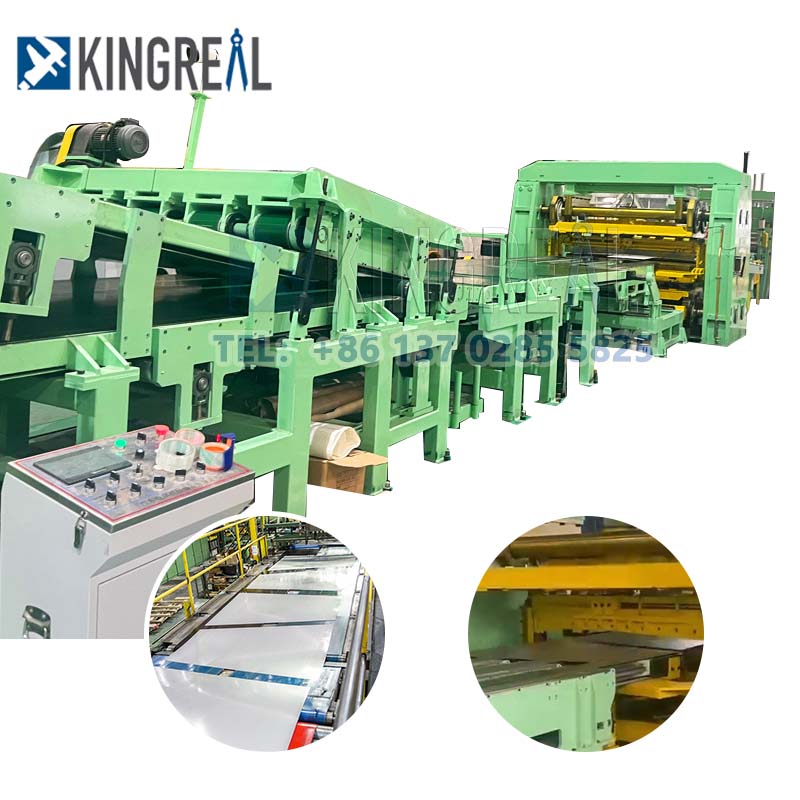
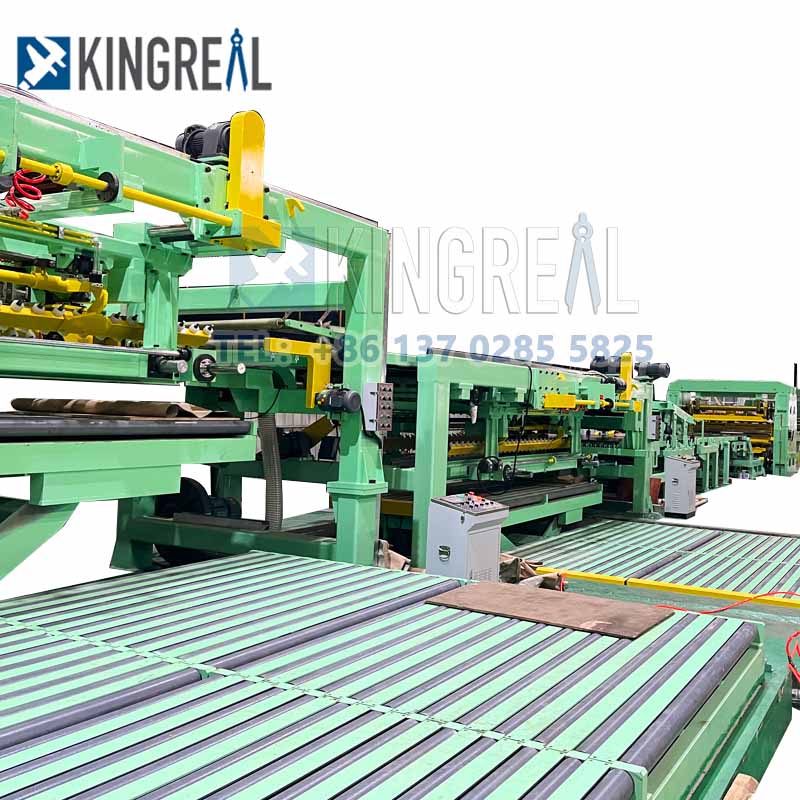
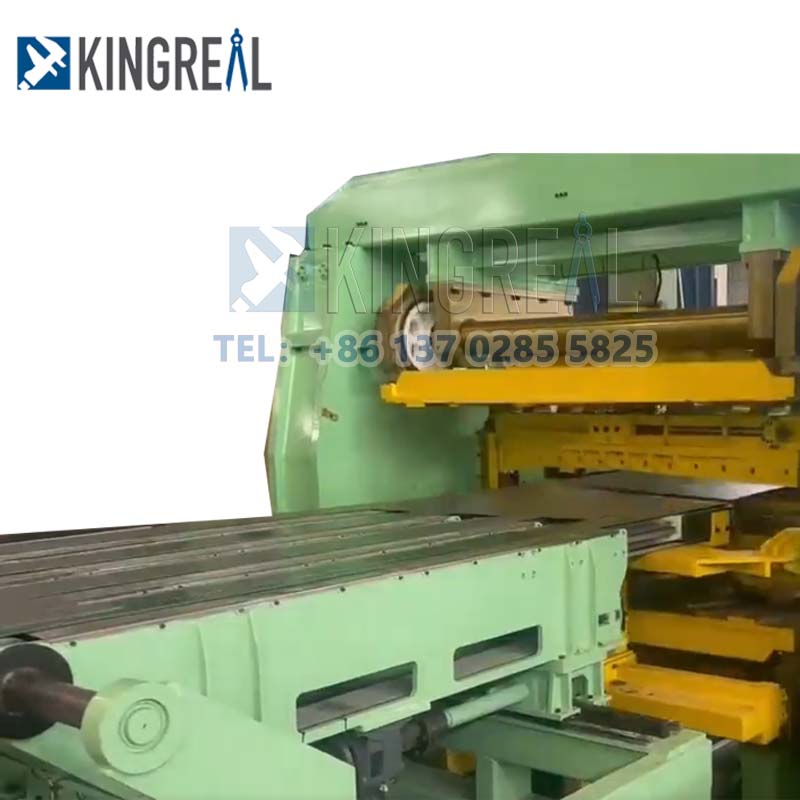
Features
- High shearing stability: The shearing action of the swing shear is stable, and the impact force on the plate is small, which is suitable for the precision shearing of thin plates.
- Compact equipment structure: The swing shear occupies a small area and is suitable for production environments with limited space.
- Moderate speed: The production speed of the swing shear is between the fixed shear and the flying shear, which is suitable for medium-speed production lines.
Application scenarios
Widely used in thin plate processing, small and medium-sized metal shearing lines or scenes with high requirements for the stability of shearing action.
3. Considerations for choosing shearing methods
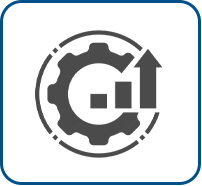
Production speed
- High-speed metal cut to length machine: flying shear or rotary shear is preferred.
- Medium and low-speed cut to length lines: suitable for fixed shear or swing shear.
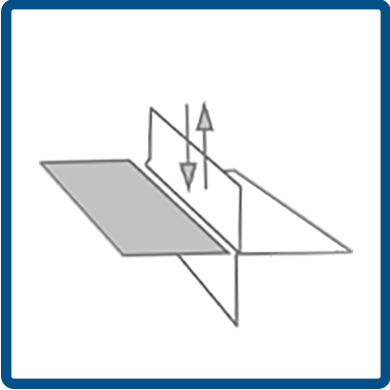
Plate thickness and material
- Thin plate: Rotary shear and swing shear are more suitable.
- Medium and thick plate: Fixed shear performs better.
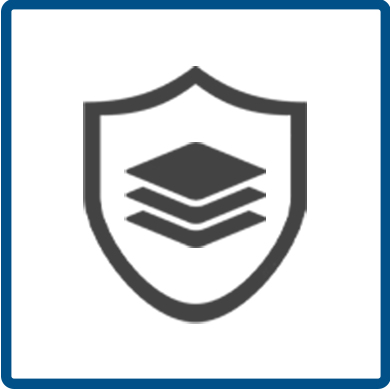
Shearing accuracy
- Fixed shear and swing shear have more advantages in scenes with high requirements for dimensional accuracy.
- Flying shear and rotary shear are suitable for continuous production with higher efficiency requirements.
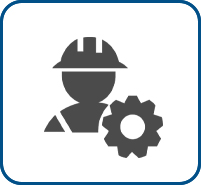
Equipment cost and maintenance
- Fixed shears and swing shears have low equipment costs and simple maintenance, which are suitable for customers with limited budgets.
- Although flying shears and rotary shears have higher costs, they are suitable for large-scale and efficient production and are more cost-effective in the long run.