Importance of precision in metal processing
In metal processing, high-precision shearing can greatly reduce waste, improve material utilization and reduce costs. In addition, precision has a profound impact on production efficiency and the final service life of the product.
In order to ensure processing accuracy, manufacturers not only need to use high-precision processing equipment, but also need to manage the processing technology in a refined manner. This is why ss stainless steel ctl machines, as an important part of modern metal processing equipment, play a vital role in processing accuracy control.
How to control cutting accuracy and size of stainless steel ctl machine?
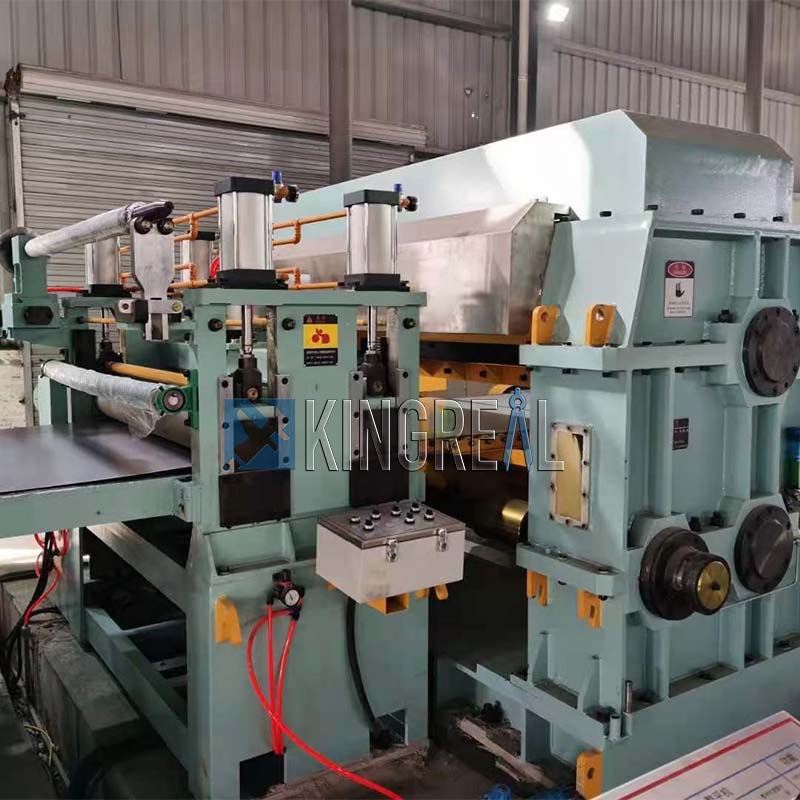
Fully automated equipment improves cutting accuracy
The introduction of fully automated ss cut to length production lines has significantly improved the accuracy of metal processing. Compared with traditional manually operated equipment, automated equipment can provide higher accuracy and stability when cutting.
Automated stainless steel ctl machine are usually equipped with advanced control systems and sensors, which can monitor and automatically adjust various parameters in the shearing process in real time, thereby effectively controlling the dimensional error of the metal plate.
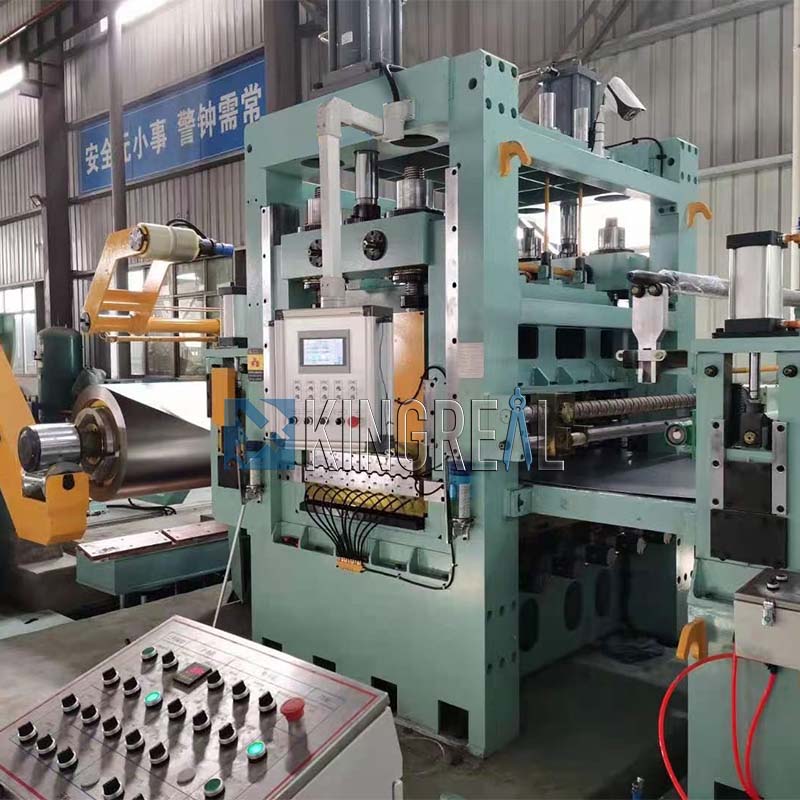
Precise adjustment of parameters
The control panel of the stainless steel cut to length line is the core interaction platform between the operator and the equipment. On the control panel, the operator can set and adjust multiple key parameters, including shear length, plate thickness, cutting angle, feed speed, etc. The setting of these parameters directly affects the shearing accuracy.
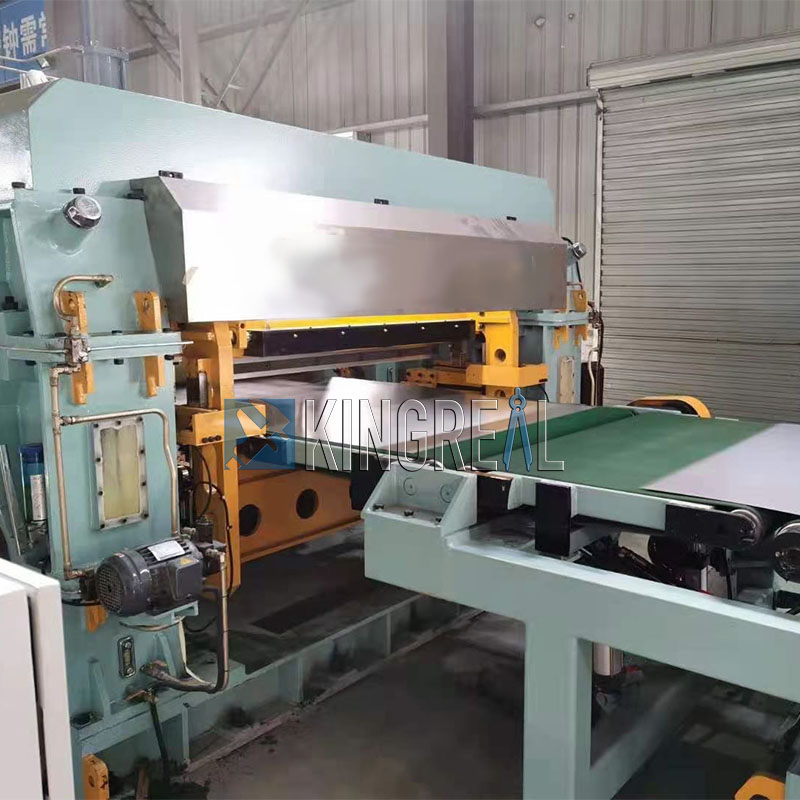
High-precision tools and cutting systems
The tool design of the ss cut to length production line also has an important impact on the processing accuracy. High-precision tools usually use carbide or high-wear-resistant materials.
These tools not only have a long service life, but also maintain stable cutting performance in high-intensity processing. Precision tool design can greatly reduce the material deformation caused by the cutting process and maintain the precise size of the plate.
Advantages of using high-precision stainless steel ctl machine
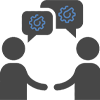
Improve product quality
High-precision stainless steel cut to length lines can ensure that the size and shape of metal plates are accurate, which directly improves the quality of products.
In areas that require high-precision processing, such as automotive manufacturing, aerospace, precision instruments and home appliances, the use of high-precision ss cut to length production lines can greatly reduce the risk of unqualified products, improve the company's product qualification rate, and enhance market competitiveness.
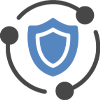
Reduce material waste
In traditional shearing processing, large dimensional errors often lead to material waste, especially when processing high-priced metal materials, the waste is more obvious.
High-precision ss cut to length production lines can effectively reduce material waste and improve material utilization by precisely controlling the cutting size. This not only helps to reduce production costs, but also helps to achieve environmentally friendly production and reduce resource waste.
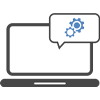
Improve production efficiency
High-precision stainless steel ctl machine can complete high-quality cutting work in a shorter time. The efficient operation of the automation system enables the equipment to run continuously at a stable speed while improving production flexibility.
During mass production, operators can quickly adjust parameters through the control panel to adapt to different production needs, reduce downtime, and improve production efficiency.
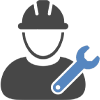
Extend equipment life
The design and material selection of high-precision stainless steel cut to length lines enable the equipment to maintain high stability during long-term operation. The precise transmission system and high-quality tools can not only ensure processing accuracy, but also reduce equipment wear and extend the service life of the equipment.
The stability and durability of the equipment also reduce the maintenance and downtime costs caused by failures.